Just How Tank Welding Inspection Avoids Future Structural Failings
Just How Tank Welding Inspection Avoids Future Structural Failings
Blog Article
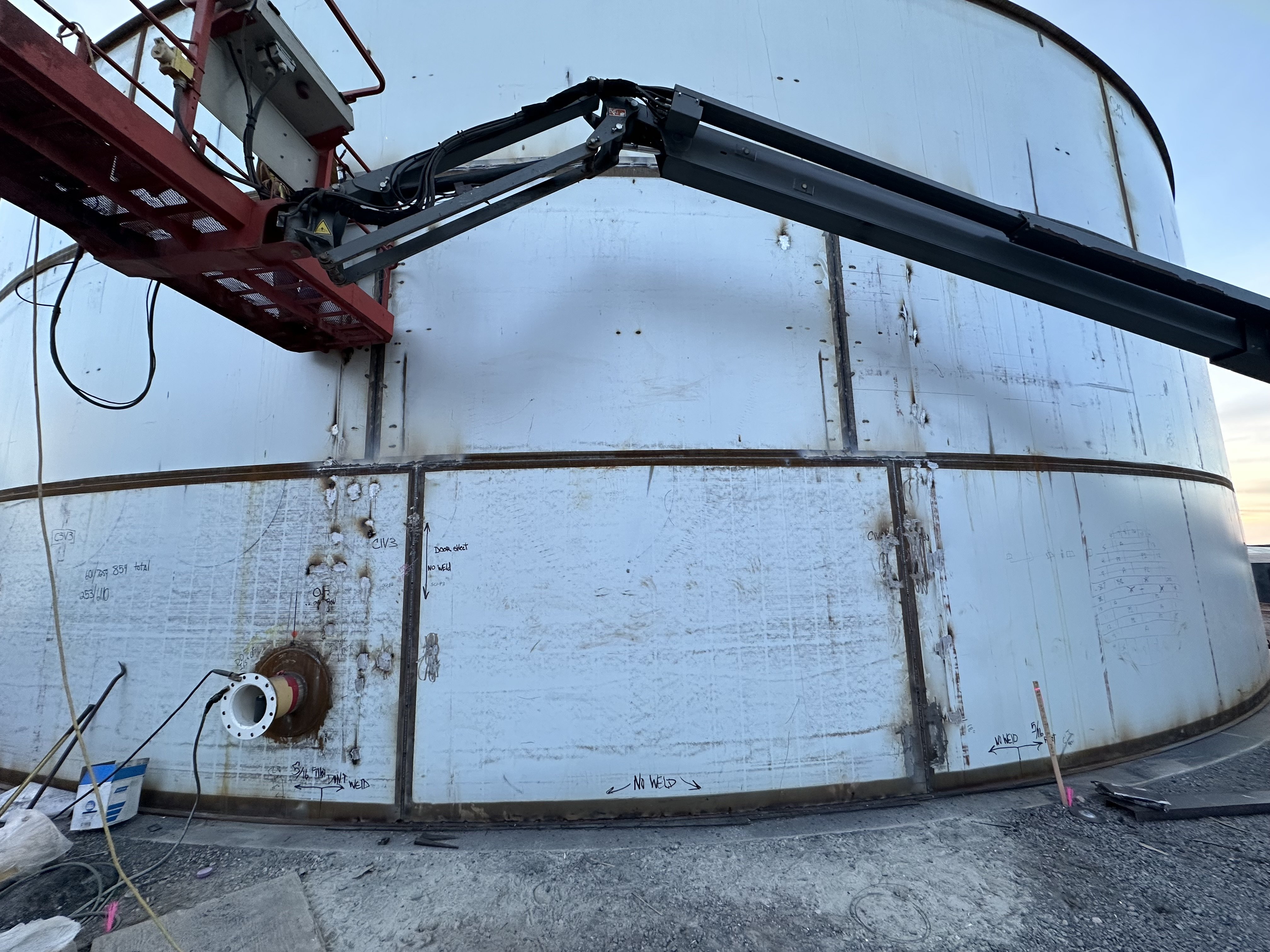
Recognizing the Significance of Rigorous Container Welding Assessment Processes in Fighting Failings and Enhancing Lifespan
In the realm of industrial operations, the relevance of strenuous container welding evaluation processes can not be overemphasized. By executing different inspection approaches, companies can detect defects early, therefore staying clear of costly repercussions and extending the life of their storage containers.
Significance of Welding Examinations
Identifying the crucial function of welding evaluations in maintaining architectural integrity, these procedures make certain that welds satisfy well established criteria and specifications - Tank Welding Inspection. Effective welding assessments are extremely important in the building and upkeep of storage tanks, as they straight affect the toughness and safety of the structures. By identifying potential deficiencies, such as incorrect strategies or product flaws, assessments minimize the danger of tragic failures
Welding evaluations encompass numerous methodologies, consisting of visual assessments, non-destructive screening (NDT), and evaluations of welding procedures. Each technique offers to confirm the high quality and conformity of welds with industry guidelines, consequently protecting both personnel and ecological interests. Regular assessments foster a culture of liability and excellence within the workforce, guaranteeing that all group members adhere to ideal methods.
Moreover, these evaluations add to the total lifecycle management of storage tanks by identifying wear or deterioration early at the same time. By dealing with these concerns proactively, organizations can prolong the functional life-span of their assets, ultimately resulting in set you back financial savings and improved integrity. In summary, the relevance of welding assessments can not be overstated; they are vital for making certain safety, longevity, and conformity in storage tank construction and upkeep.
Typical Reasons For Storage Tank Failings
Understanding the usual root causes of tank failures is vital for stopping tragic cases and guaranteeing the durability of storage systems. One prevalent cause of tank failing is corrosion, which can considerably compromise the structural integrity of tanks in time. Environmental aspects, such as exposure to dampness, chemicals, and temperature level variations, can accelerate this procedure.
One more crucial factor is inappropriate welding methods, which may bring about defects like cracks or insufficient joints. These problems can jeopardize the container's toughness and bring about leaks or ruptures. Furthermore, inadequate maintenance methods can result in undetected damage, eventually raising the risk of failing.
Design imperfections, consisting of insufficient thickness or bad material choice, can additionally contribute to storage tank susceptabilities. Additionally, operational elements, such as overfilling or direct exposure to severe pressures, can stress the container past its designated restrictions.
Trick Evaluation Methods
Effective assessment strategies play a crucial function in minimizing the threats connected with tank failings. A thorough approach to container welding assessment includes several key techniques, each designed to identify possible problems and make sure architectural stability.
Visual inspection continues to be the very first line of protection, permitting assessors to recognize surface area anomalies such as cracks, deterioration, or imbalance. This method is typically supplemented by non-destructive screening (NDT) techniques, which are crucial for analyzing weld top quality without jeopardizing the container's honesty.

In addition, magnetic fragment screening (MPT) and dye penetrant testing (DPT) are efficient for spotting surface problems in ferromagnetic products and non-porous surfaces, respectively. Each method has its toughness and constraints; as a result, a mix of methods is usually used to attain comprehensive evaluation results.
Benefits of Extensive Evaluations
While the prompt costs of rigorous evaluations may seem challenging, the long-lasting advantages dramatically exceed these first financial investments. Implementing complete assessment refines not only improves the stability and security of container frameworks however also decreases the danger of catastrophic failures that can lead to substantial financial losses and ecological injury.
Strenuous evaluations aid identify potential concerns early in the welding procedure, permitting prompt corrective actions that avoid pricey repair services or replacements down the line. This positive method cultivates a culture of quality control, where adherence to ideal practices ends up being ingrained in functional treatments. Moreover, routine assessments contribute to enhanced possession durability, as they make sure that tanks remain in optimum condition throughout their life-span.
Furthermore, the documentation produced from these evaluations works as a useful source for upkeep planning and performance assessments. This data-driven method can additionally boost description operational effectiveness, resulting in reduced downtime and boosted efficiency. Inevitably, strenuous evaluations not only guard Discover More the architectural stability of tanks but additionally supply substantial financial advantages, enhancing the notion that buying top quality assurance is a smart decision for any kind of organization associated with storage tank procedures.
Regulatory Specifications and Conformity
Regulative requirements and compliance are important components of storage tank welding assessment procedures, as they establish the framework for making sure safety and security and quality in operations. Conformity with these requirements not only mitigates threats yet also improves the general honesty of welded structures. Different companies, including the American Society of Mechanical Engineers (ASME) and the American Petroleum Institute (API), provide standards that determine appropriate practices for welding, evaluation, and screening.
These criteria mandate using certified employees, the application of extensive assessment methods, and adherence to particular welding treatments. By straightening with governing needs, companies can ensure that their tanks fulfill the necessary safety and performance criteria, thereby decreasing the likelihood of devastating failures that check out this site can result in significant financial losses and environmental damages.

Moreover, regulative compliance fosters a society of accountability and constant improvement within the welding and fabrication fields (Tank Welding Inspection). Regular audits and examinations make certain that techniques stay aligned with progressing criteria, therefore promoting long-term integrity and operational efficiency. Eventually, adherence to regulatory standards not just protects properties but also improves the lifespan of bonded storage tanks, guaranteeing they serve their designated objective successfully with time
Verdict
In conclusion, extensive tank welding examination procedures play a crucial duty in preventing failures and extending the life-span of storage frameworks. By determining prospective shortages through various assessment methods, companies can reduce dangers associated with storage tank honesty.
Report this page